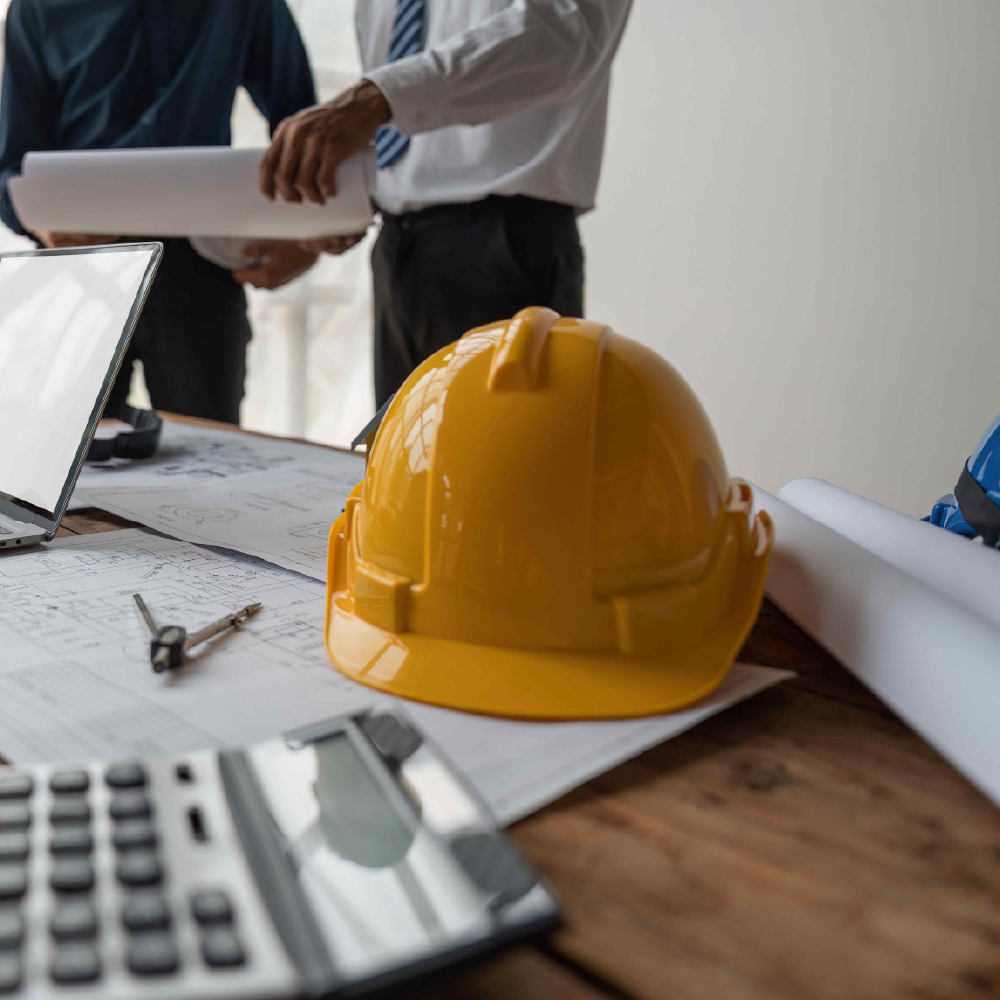
Overhead costs in construction are often considered the “silent drain” on profitability. These indirect expenses, though necessary for running a business, can quickly erode profit margins if not effectively managed. Overhead costs in construction include administrative salaries, insurance, equipment depreciation, and utilities, among other expenses. While direct project costs can be easier to track and manage, overheads often go unnoticed or unchecked until they significantly impact the bottom line.
Successfully managing overhead costs without sacrificing operational efficiency is crucial for construction firms of all sizes. The strategies that follow focus on ways to minimize overhead costs, improve operational efficiency, and ensure long-term profitability.
Understanding Overhead Costs in Construction
Before delving into strategies for managing overhead, it’s essential to understand the types of overhead costs specific to the construction industry. These expenses are typically divided into two categories: fixed and variable overheads.
Fixed Overhead Costs: These costs remain constant regardless of project size or workload. Examples include office rent, administrative staff salaries, insurance, and property taxes.
Variable Overhead Costs: These fluctuate based on project activity. Variable overheads can include fuel, temporary project office costs, communication expenses, and equipment maintenance.
The challenge for construction companies lies in controlling these costs without compromising the quality of work or delaying project timelines.
Accurate Budgeting and Estimation
One of the most important steps in managing overhead costs is creating accurate project budgets and estimates. Underestimating costs at the beginning of a project can lead to budget overruns, eating into profits and making it difficult to cover overhead expenses.
To prevent this, construction managers should adopt precise cost-estimating practices. This includes factoring in not only direct costs but also potential overheads like insurance, administrative support, and equipment depreciation. Additionally, leveraging construction management software can help streamline this process by providing real-time data on labor, material, and overhead costs. Regularly reviewing historical data from previous projects can also improve the accuracy of cost predictions.
Implementing Technology for Cost Control
The construction industry has been slower than others to embrace technology, but recent innovations can help companies better manage overhead expenses. Construction management software, project tracking tools, and digital payroll systems are just a few examples of technology that can optimize operations.
Project Management Software: This software enables managers to track the progress of a project in real-time, monitor expenses, and allocate resources more effectively. By identifying inefficiencies early, project managers can make adjustments before they result in unnecessary overhead costs.
Digital Payroll Systems: Automating payroll reduces human error and can streamline the process of managing variable labor costs, ensuring workers are paid correctly and on time. This reduces the likelihood of disputes and unnecessary payroll adjustments that could inflate overhead costs.
Cloud-Based Collaboration Tools: Using cloud-based platforms for communication and document sharing reduces the need for physical meetings and paperwork. This can lower overheads like travel costs, printing expenses, and time spent on administrative tasks.
Outsourcing Non-Essential Services
Outsourcing non-core functions is an effective way to manage overhead costs without sacrificing service quality. Rather than hiring full-time employees for tasks like accounting, payroll management, or IT support, many construction firms are turning to third-party providers who specialize in these areas.
Accounting and Payroll: By outsourcing financial functions, construction companies can reduce the costs associated with hiring and training in-house staff, while ensuring that their financial operations are handled by professionals.
IT Services: Maintaining an in-house IT department can be costly, especially for smaller construction companies. Outsourcing IT support allows firms to access top-tier technology and expertise without the overhead costs of full-time staff.
Administrative Support: Virtual assistants or part-time administrative support can be a cost-effective solution for firms that do not require a full-time administrative team. This reduces payroll overhead while ensuring that day-to-day operations run smoothly.
Optimizing Equipment and Resource Allocation
Construction firms often spend large sums on equipment purchases, maintenance, and storage costs that directly contribute to overhead. Optimizing equipment usage is a key strategy for reducing these expenses.
Leasing vs. Purchasing: Depending on the size of a company and the frequency of equipment use, leasing may be a more cost-effective option than purchasing. Leasing eliminates the need for large upfront investments and reduces maintenance and storage costs.
Sharing Equipment: Some firms collaborate with other construction companies to share equipment. This approach can help avoid unnecessary purchases and ensure that expensive machinery is used to its full capacity.
Preventative Maintenance: Regularly scheduled maintenance can prevent costly breakdowns and reduce the risk of project delays. Investing in preventative maintenance ensures that equipment is always in top working condition, which can ultimately reduce long-term costs.
Reducing Energy and Utility Expenses
Utilities such as electricity, water, and fuel are often overlooked as sources of overhead costs in construction. Implementing energy-efficient practices on job sites and in offices can help reduce these expenses significantly.
Energy-Efficient Equipment: Investing in energy-efficient machinery and tools can reduce fuel consumption and lower long-term operating costs. For example, electric-powered equipment may be more expensive upfront but can result in savings on fuel and maintenance over time.
On-Site Power Generation: For remote construction projects, using solar panels or wind turbines to generate power on-site can reduce the need for expensive fuel deliveries and lower utility costs.
Energy Audits: Conducting regular energy audits at both the office and job sites can help identify areas where energy consumption can be reduced, such as lighting, heating, and cooling systems.
Streamlining Administrative Processes
Administrative costs, such as paperwork, permits, and compliance, are another area where overhead can balloon. Streamlining these processes can improve efficiency and cut down on unnecessary expenses.
Digital Documentation: Moving from paper-based to digital documentation reduces printing costs, eliminates the need for physical storage, and improves data accessibility. Additionally, digitizing forms can speed up the approval process for permits, reducing project delays.
Centralized Reporting: Using a centralized system for project reporting ensures that all stakeholders have access to the same data. This reduces the time spent on administrative follow-ups and ensures that decisions are made based on accurate, up-to-date information.
Automating Compliance Management: Compliance with local regulations and safety standards is essential, but managing it manually can be costly and time-consuming. Automation tools can simplify the process by tracking regulatory changes, maintaining records, and alerting managers to upcoming deadlines.
Continuous Training and Skill Development
Investing in employee training and skill development can significantly reduce overhead in the long run. Well-trained employees are more productive, make fewer mistakes, and require less supervision, which helps reduce both labor costs and management overhead.
Cross-Training Employees: Cross-training employees to handle multiple roles within a project can minimize the need for specialized staff and reduce payroll expenses. This flexibility ensures that labor resources are used efficiently, especially during slower periods or smaller projects.
Safety Training: Reducing workplace accidents through regular safety training can lower insurance premiums and avoid costly project delays. Accidents not only increase insurance claims but can also lead to equipment damage and lost productivity.
Managing overhead costs in construction requires a proactive approach that combines accurate budgeting, the use of technology, and strategic resource allocation. By understanding the nature of overhead expenses and implementing cost-saving measures like outsourcing, energy efficiency, and employee training, construction firms can optimize operations without sacrificing quality or safety.
Efficiency in overhead management is not about cutting corners; it’s about finding smarter ways to allocate resources, reduce waste, and improve productivity. In an industry where profit margins are often razor-thin, these strategies can make the difference between profitability and financial strain. By taking control of overhead costs, construction companies can ensure their long-term success and stability in a competitive market.